The Robot Revolution: The Top 10 Robotics Applications
Outstripping projected growth rates year after year, the global robotics market is expected to cross the $100 billion mark within the next five years.
Falling prices, improved safety and performance, and more interoperable components and software are fueling the surge in demand. Moreover, robotic technology is converging with advancements in other areas, including machine vision, haptics, and voice technology, expanding the scope of applications and tasks robots can achieve.
As robots and artificial intelligence further penetrate new industries, they will become an even more integral part of our daily lives. Understanding these new use cases and their facilitating technologies provides insight into the anticipated future directions and challenges for companies looking to drive the robotics revolution.
Based on data from 2019 World Robotics Report, we share the leading segments within robotics, their top challenges, and the innovations that can accelerate their adoption.
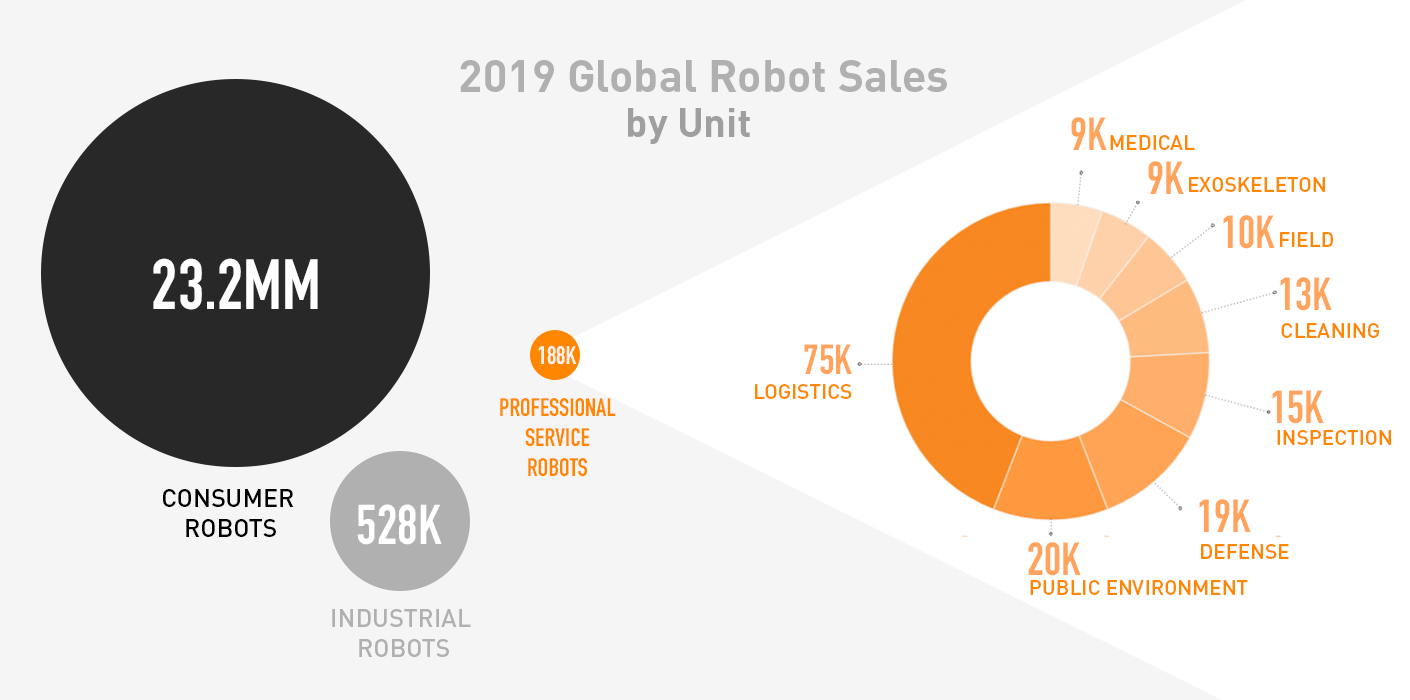
10. Medical Robots
Though making up a small percentage of professional service robots sales, medical robots constitute 30% of the industry’s revenues with a market worth US$3.7 billion. Surgical robots, like MANTA client’s Medrobotics Flex or Johnson & Johnson’s Auris, enable minimally invasive access to hard-to-reach anatomical locations. They can also be more precise than surgeons and reduce fatigue, especially for repetitive tasks like suturing, thereby reducing errors.
The Challenge
Many current surgical systems lack sufficient and accurate haptic feedback, which surgeons otherwise use to navigate, detect lesions, and gauge force. Harnessing the power of miniaturized actuators and designing human-centered force feedback algorithms through ergonomic assessments can improve accuracy and dexterity while minimizing trauma to the patient.
The Innovation
Reusable touch sensors require miniaturization, biocompatability, autoclavability to prevent cross-contamination. As the price of such sensors falls, companies can afford to increasingly embedding disposable into surgical robotic arms to differentiate their offering. Researchers like those at MIT’s MCube Lab, which spun out our client Gelsight, are also developing and testing the utility of vision-based tactile sensors that can be used to measure the texture and topography of tissue.
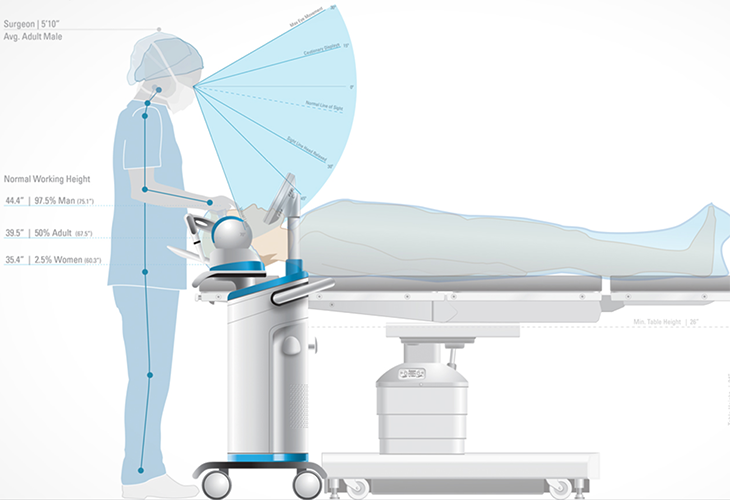
In designing the Medrobotics Flex Surgical System, our ergonomic analyses led to the development of a system that could reduce physical strain, a common user complaint that can lead to increased errors.
9. Exoskeletons
In 2019, sales of powered human exoskeletons increased by over 25%, making up 3% of all professional service robots sold. While mainly used in rehab services, exoskeletons are also meeting a need in military and warehouse applications. Sarcos’ Guardian XO, for example, can offload the tasks that strain or injure warehouse workers while increase productivity by up to a factor of 10.
The Challenge
The main challenge for roboticists developing exoskeletons is to work with the constraints and power of the human body, rather than against it. Given that exoskeletons must be wearable for an extended time, they need to particularly have a high strength-to-weight ratio. This can be achieved by compact design and leveraging the strength of the body.
The Innovation
In developing the BionX emPOWER ankle prosthetic with MIT’s Hugh Herr, MANTA harnessed sensors and microprocessors to adapt the prosthetic to the user’s walking, transferring greater energy to propel them forward. With elegant system architecture and materials selection, our engineers and designers were able to fit these powerful components into a lightweight prosthetic sized to fit within a shoe.
Other researchers, such as the Wyss Institute’s Conor Walsh, use sensor-controlled pneumatic tubing to create soft, lightweight exosuits that synergistically augment the wearer’s biomechanics. Of course, the continued challenge of these advances is transforming prototyped concepts into commercially manufacturable products.
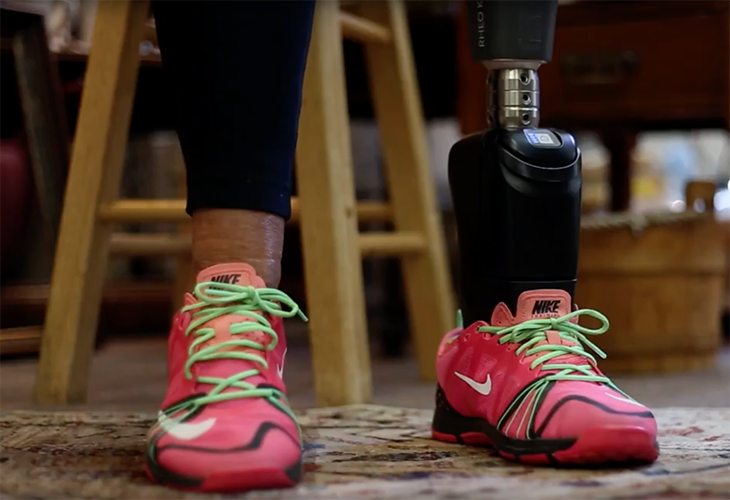
Compact engineering design of the emPOWER ankle prosthesis enabled it to be more power-efficient while still actively powering the user's walk.
8. Field Robots
Sales of field robots has grown 8% within the past year, making up nearly 4% of professional service robot sale Within this segment, drones can be used to scan fields aerially to measure crop yields and health, or to herd or search for animals. Meanwhile, harvesting robots, like those developed by Vision Robotics, use mature vision algorithms and statistical analyses to estimate crop loads and cultivate and harvest produce, including automation of grapevine pruning, lettuce thinning, and berry picking.
The Challenge
Harvesting in particular poses a challenge for robots because of the complexity of the task, as well as the rather low costs of human labor in the industry. Picking, especially of delicate items such as fruits, is challenging due to the dexterity and precision required.
The Innovation
In developing picking robots, our engineers have worked with vision software systems that allow robots to identify a variety of items. By testing different end-effectors, including soft grips like those produced by Soft Robotics, we have trained robots to pick oddly-shaped and delicate items like fresh produce.
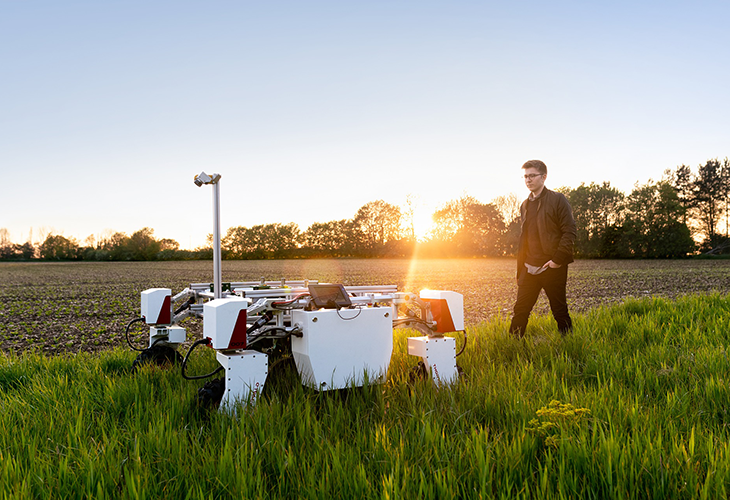
Agricultural robots equipped with machine vision can scan large tracts of land to estimate crop yield and health, while also performing tasks related to cultivating and harvesting.
7. Professional Cleaning Robots
Boosted by the pandemic, professional cleaning and disinfecting robots are being deployed worldwide to sterilize hospitals, offices, and food banks. More resource and time-efficient than human cleaners, UV-disinfection robots are particularly safer and more cost-effective for large, heavily-trafficked areas.
The Challenge
Like logistics robots, professional cleaning robots need to accurately map the environment they’re in, with particular caution to not operate around humans if emitting UV-C. When moving around an area, these robots must also be able to adjust speed to ensure the recommended disinfecting dosage is applied to surfaces and new objects around them.
The Innovation
Companies operating in the warehouse and public environment spaces, such as Corvus Robotics, have translated their engineering capabilities into developing cleaning robots. These rolling mobile robots are initially driven by an operator remotely driving the robot to map the area using sensors. The robot subsequently follows pre-programmed waypoints from this mapping to navigate the area for cleaning. As machine vision improves, these robots will continue to gain autonomy in navigating.
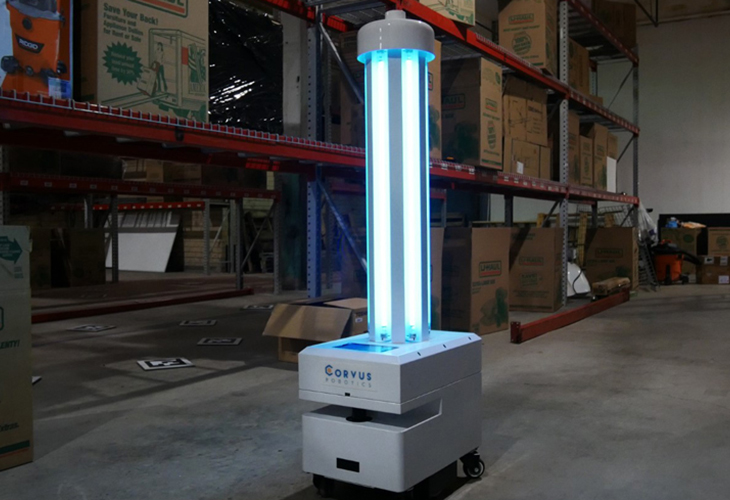
UV-C disinfecting robots, like this model from Corvus, can be used to autonomously prevent hospital-acquired infections and sanitize large, crowded areas.
6. Inspection Robots
Robotic solutions for inspection and maintenance, such as those sold by Avitas Systems, have seen a tremendous increase in recent years, dominated by the need for mobile, automated inspection of high-value infrastructure in oil and gas.
Unlike humans, inspection robots are built to navigate through narrow areas and operate in precarious environments under high pressure or temperature. They can also continuously collect images from structures, enabling more preventative maintenance and planning for outages.
The Challenge
The design of inspection robots is often use case-specific, reducing their adaptability across a wide variety of inspection needs. Additionally, more than other robots, they require greater dexterity, as well as robust adhesion and grasping mechanisms to crawl, climb, or snake through complex structures.
The Innovation
Modular inspection robots, like the crawlers developed by Inuktun, allow customers to outfit robots with various tracks, cameras, and sensors to perform a diversity of inspection tasks. Conducting a systems-level analysis and considering all potential use cases in the design cycle allows companies to develop more cost-effective robots with plug-and-play cameras and sensors, including audio, pulsed array, and ultrasound, to expand the diversity of tasks an inspection robot can perform.
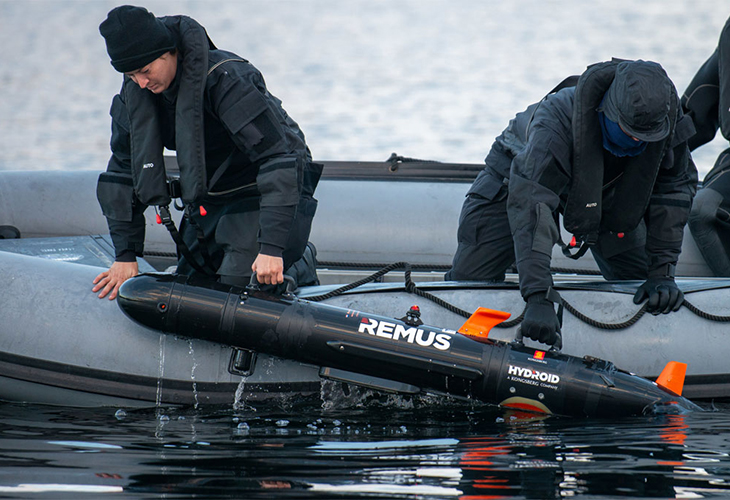
Hydroid's fleet of autonomous underwater vehicles have numerous applications in defense, search and rescue, and underwater inspection for offshore drilling.
How Will Your Robot Transform Industries?
Our experienced team of researchers, designers, and engineers can help you create a standout user experience, iconic forms, and cutting-edge electromechanical and perception solutions for your robot - no matter the industry. Get started now.